Le picking logistique est étape cruciale de la chaîne logistique. Cette activité consiste à prélever dans les entrepôts des articles ou des produits afin de les préparer à l’expédition. L’efficacité opérationnelle de l’entrepôt va dépendre du processus de picking logistique. De cette efficacité va souvent dépendre également la rentabilité de l’entreprise, mais également la satisfaction client. Nous allons voir ensemble les principaux types de picking. Nous examinerons leurs avantages respectifs mais aussi leurs inconvénients. Enfin, nous aborderons les bonnes pratiques à mettre en place afin d’assurer la sécurité des opérateurs de picking logistique.
Sommaire
Qu’est-ce que le picking ?
Le picking logistique a pour objectif de sélectionner et de prélever dans un entrepôt des produits, articles ou marchandises afin de les préparer pour une expédition. Tout le monde a en tête les images de ces immenses entrepôts des géants du e-commerce dans lesquels s’affairent des dizaines d’opérateurs pour aller chercher les marchandises référencées et préparer la commande d’un client. Mais le picking logistique n’est pas utilisé que dans le e-commerce. Toute activité nécessitant le stockage et l’utilisation de produits dans un entrepôt est concerné.
Il existe différents types de picking logistique afin de répondre aux besoins en fonction de la taille, du poids, de la nature et de la quantité des articles à prélever.
Les différents types de picking
Le picking manuel
Il s’agit du type de picking le plus répandu. C’est aussi le plus simple. L’opérateur se déplace dans l’entrepôt afin de prélever les différents articles à la main. La liste des articles à collecter peut se trouver sur un document papier ou être accessible via un terminal mobile. En fonction de la taille de l’entrepôt et des marchandises, l’opérateur peut se déplacer à l’aide d’un chariot ou d’un transpalette par exemple.
Le picking manuel a l’avantage d’être extrêmement simple à mettre en œuvre. Il ne nécessite pas d’équipement particulier ni d’aménagement de l’entrepôt. Il est adapté aux marchandises suffisamment légères et de petite taille.
Le picking manuel présente en revanche un certain nombre d’inconvénients. En effet, l’opérateur va devoir effectuer de nombreux déplacements dans l’entrepôt et chercher les articles dans les rayonnages. La productivité du picking manuel est donc assez faible. De plus, le prélèvement des articles dépendant uniquement de l’opérateur, même s’il suit une liste, le risque d’erreur est élevé. Enfin, l’opérateur peut être amené à soulever des charges lourdes et adopter des postures pouvant entraîner des problèmes de santé à plus ou moins long terme.
L’organisation de l’entrepôt doit donc être particulièrement soignée afin de contrebalancer au moins une partie de ces inconvénients. Les produits peuvent par exemple être regroupés dans différentes catégories et identifiés grâce à des étiquettes claires (codes barres, RFID). Les opérateurs doivent également être sensibilisés aux gestes et postures à adopter. Ils doivent enfin disposer d’équipements de protection individuelle efficaces : casque, gants, chaussures de sécurité ou encore équipement de protection antibruit.
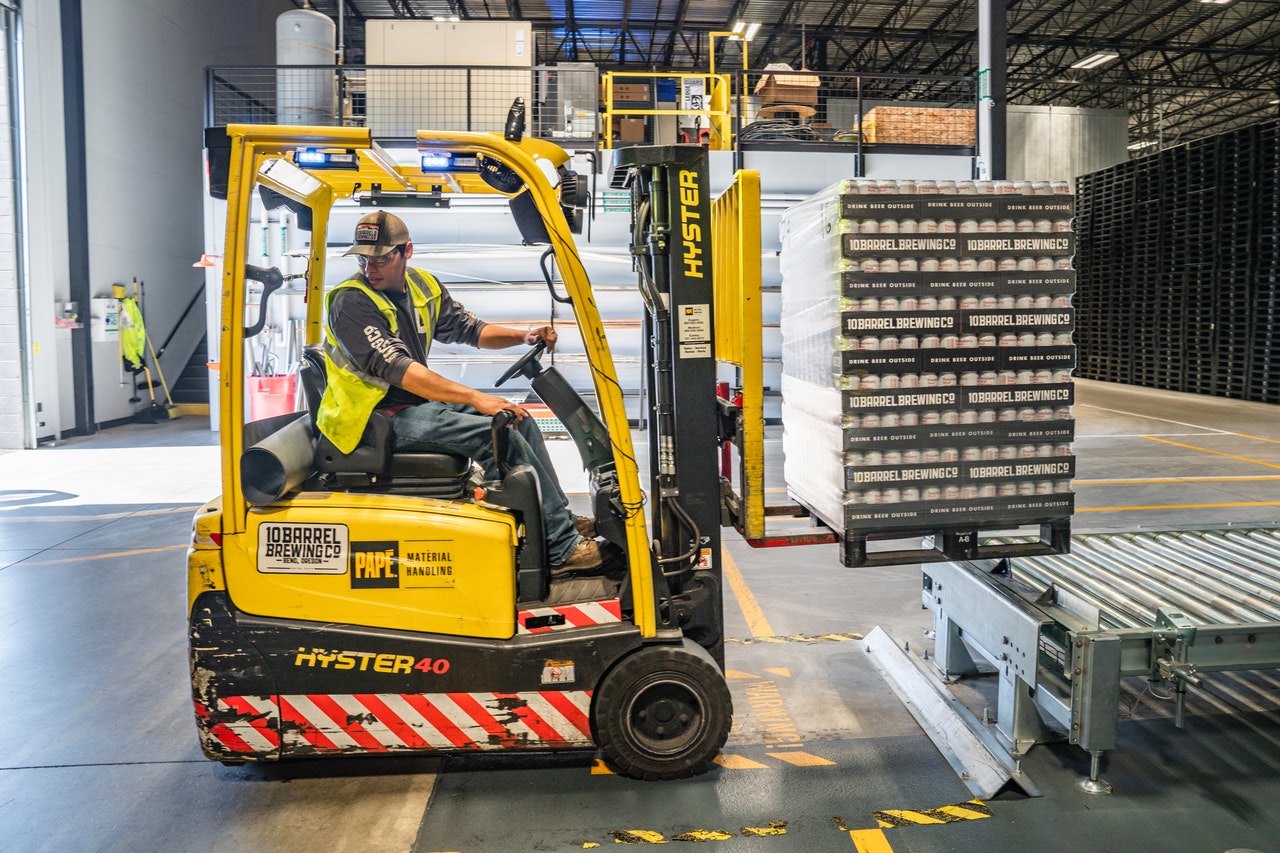
marquage au sol entrepot logistique
Le picking par zone
Cette variante du picking manuel consiste à diviser l’entrepôt en zones. Chaque opérateur est affecté à une zone bien précise, et une seule. Pour chaque commande ou expédition à préparer, l’opérateur va chercher dans sa zone les articles commandés qui s’y trouvent. L’ensemble des articles d’une commande sont ensuite regroupés dans une zone réservée à cet effet. Cette zone est également appelée « zone de consolidation ».
Le picking par zone améliore grandement la productivité des opérateurs et donc de l’entreprise par rapport au picking manuel. Les déplacements de l’opérateur sont fortement réduits. Le nombre de produits prélevés par heure augmente très sensiblement et le risque d’erreur en revanche diminue fortement, d’autant plus si on limite le nombre d’articles qu’un opérateur doit prélever à chaque fois. Le picking par zone reste efficace lorsque les articles sont imposants ou lourds. Il est d’autant plus efficace pour gérer des commandes nombreuses ou présentant de nombreux points communs.
Le picking par zone présente également un certain nombre d’inconvénients. L’organisation des articles dans l’entrepôt est bien plus complexe et nécessite une surface plus importante. Une gestion automatisée des commandes est indispensable afin de vérifier les listes d’articles, leur localisation et de coordonner le travail des opérateurs. Ces derniers peuvent également être amenés à régulièrement soulever des charges lourdes, avec des conséquences possibles sur leur santé.
Les zones de picking doivent donc être parfaitement définies et identifiées. Les articles doivent être disposés en tenant compte de leur taille, de leur encombrement et de la fréquence à laquelle ils sont prélevés. Des systèmes d’aide à la préparation, disponibles sur des écrans tactiles, peuvent par exemple guider les opérateurs et les aider à vérifier les prélèvements d’articles à effectuer. Les opérateurs doivent bien entendu être équipés de protections individuelles adaptées à leur activité.
Le picking par batch
Autre variante du picking manuel, le picking par batch consiste à regrouper les commandes et à prélever l’ensemble des articles en une fois. Le nombre de produits prélevés à chaque fois étant potentiellement beaucoup plus important, les opérateurs vont utiliser des équipements adaptés comme des chariots à plusieurs niveaux par exemple. Les articles de chaque commande seront séparés sur les différents niveaux. A la fin du prélèvement, les commandes peuvent être séparées puis expédiées indépendamment.
Le picking par batch va permettre d’optimiser le temps de préparation. Il limite les déplacements des opérateurs en leur permettant de traiter plusieurs commandes simultanément. Le contrôle des articles prélevés est également facilité et le risque d’erreur réduit. Le picking par batch est plus adapté aux commandes variées contenant des produits petits et légers.
Les principaux inconvénients du picking par batch viennent de la nécessité d’utiliser du matériel spécifique nécessaire ainsi que des gestes et mouvements parfois pénibles que doivent réaliser les opérateurs.
Afin de réduire ces inconvénients, il est important de définir finement les critères de regroupement des commandes. Les articles doivent être clairement identifiés et identifiables.
Le picking automatisé
Le picking automatisé est né pour réduire la pénibilité du travail, améliorer les performances et réduire les risques d’erreur. Il consiste à utiliser des robots et des automates pour prélever les articles dans l’entrepôt. En supprimant les interventions humaines, le picking automatisé va permettre d’augmenter la productivité de façon très significative. Les automates peuvent fonctionner 24h/24 et 7 jours/7, en éliminant le risque d’erreur et en assurant la traçabilité des articles. Pour être manipulés par les robots, les produits ne doivent cependant pas être trop gros ni trop lourds. Ils peuvent traiter des commandes nombreuses et se ressemblant avec beaucoup d’efficacité.
Le picking automatisé nécessite par contre un investissement assez important. Le matériel va donc être amorti sur le long terme et le nombre de commandes traitées doit être important afin que l’investissement soit rentable. Il est également impératif de mettre en place des opérations de maintenance préventive et d’avoir une maintenance corrective très efficace. En effet, tout étant automatisé, sans intervention humaine possible, toute panne peut entraîner l’arrêt de l’activité et donc des pertes financières pour l’entreprise.
Compte tenu de l’investissement nécessaire, il est important de bien prendre en compte le volume de commandes à traiter, les types de produits à prélever, la fréquence à laquelle les opérations sont réalisées ainsi que la configuration de l’entrepôt. Les robots et automates choisis doivent être adaptés en fonction des opérations à réaliser : navettes, convoyeurs, trieurs, robots mobiles ou à bras motorisés…
Pour conclure sur le picking logistique
Le picking logistique est au cœur de l’activité de préparation de commandes et d’expédition de produits. Chaque type de picking a ses avantages et ses inconvénients. Chaque entreprise doit donc choisir un ou plusieurs types en fonction de ses besoins réels et de ses activités.
Quel que soit le type de picking logistique mis en place dans l’entrepôt, il est impératif que les opérateurs soient correctement protégés. L’entreprise doit donc leur fournir des équipements de protection individuelle adaptés.
Si vous souhaitez protéger vos opérateurs pratiquement le picking logistique, n’hésitez pas à nous contacter. Nos experts vous assisteront afin de déterminer la solution la plus adaptée à vos besoins.
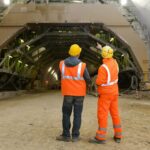
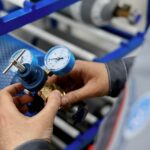

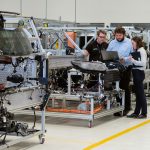
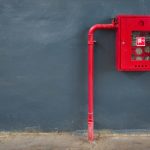
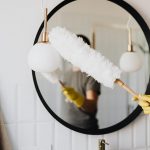