Depuis sa création, l’industrie a connu plusieurs révolutions. L’industrie 4.0, aussi désignée par les termes “entreprise 4.0” ou “manufacturing 4.0”, représente la quatrième révolution majeure. Elle est clairement caractérisée par l’utilisation et l’intégration de technologies numériques avancées au sein même des processus de fabrication. Grâce à une connectivité accrue, la production est désormais personnalisée pour une efficacité maximale. Revenons ensemble sur les progrès réalisés par l’industrie et sur ce que cette dernière révolution majeure apporte aux entreprises, mais aussi aux salariés.
Qu’est-ce que l’industrie 4.0 ?
La quatrième révolution industrielle majeure est marquée par la convergence de technologies de pointe telles que l’Internet des objets (IoT), l’intelligence artificielle (IA), la réalité augmentée et le cloud computing. L’intégration de ces technologies transforme radicalement les processus de fabrication industriels.
Désormais, tout est interconnecté, machines, systèmes informatiques et humains sont capables de communiquer et d’échanger des données en temps réel. Il ne s’agit donc pas uniquement d’automatiser des processus. Il s’agit maintenant de les rendre intelligents. Grâce à une analyse continue de l’important volume de données fourni en temps réel par l’écosystème industriel interne, les systèmes deviennent capables de s’optimiser eux-mêmes.
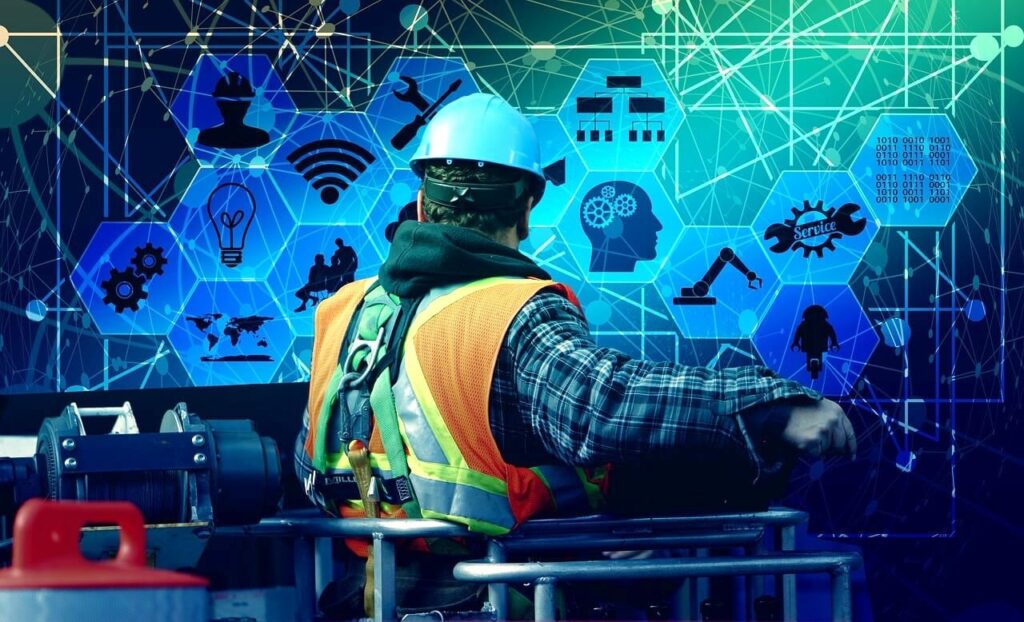
Une évolution des machines
Au sein de l’entreprise 4.0, les machines ne sont plus isolées. Elles deviennent des entités intelligentes. Les capteurs et les actionneurs dont elles sont équipées sont capables de surveiller en temps réel les conditions de fonctionnement. Il est possible de détecter les anomalies, de prédire les pannes et de mettre en place des actions de maintenance avec un minimum de répercussions sur la production.
Le système de production peut également s’adapter en temps réel en fonction de la demande, de l’état de la chaîne d’approvisionnement ou encore des conditions du marché. L’industrie du futur 4.0 garantit une flexibilité et une réactivité optimales.
Une prise de décision décentralisée
Les données sont captées et analysées en temps réel. Elles circulent librement sur le réseau constitué par l’ensemble des entités connectées grâce à l’IoT. Elles peuvent ensuite être analysées grâce à l’IA, ce qui permet aux unités opérationnelles de réagir rapidement. Il n’est plus besoin d’attendre la décision d’une autorité centrale. Désormais, les unités locales disposent de toutes les informations de terrain pour prendre les meilleures décisions. Les processus et les produits sont de plus constamment améliorés grâce aux algorithmes d’apprentissage utilisés. Plus le système collecte et analyse de données, plus il apprend et est capable d’optimiser les processus.
Une personnalisation de masse
Auparavant uniquement capable de produire en masse des produits identiques, désormais, l’industrie 4.0 est capable de personnaliser en masse sa production. Désormais, il est possible de satisfaire les exigences des clients qui recherchent un produit personnalisé avec la même efficacité que s’il s’agissait d’une production de série traditionnelle.
L’apport de technologies telles que la robotique modulaire et l’impression 3D a été déterminant. Il est possible avec le manufacturing 4.0 de configurer rapidement une ligne de production afin de l’adapter à des demandes spécifiques.
Sécurité et durabilité
Les technologies utilisées dans l’industrie 4.0 permettent d’intégrer une gestion de la sécurité bien plus efficace. La collecte et l’analyse en temps réel d’un volume important de données provenant des capteurs installés sur la chaîne de production permettent d’anticiper les risques et de prévenir les accidents.
L’analyse avancée des mêmes données permet d’optimiser les ressources nécessaires à la production. Les quantités de déchets produits et de pertes sont considérablement réduites grâce à une optimisation des approvisionnements et de la consommation des matières premières.
Chronologie des évolutions jusqu’à la quatrième révolution industrielle
La première révolution industrielle
La première révolution industrielle date de la fin du 18ème siècle qui a vu le développement de la machine à vapeur et le début de la mécanisation. Des usines ont été construites, les processus manuels ont été mécanisés et la société est passée à une économie industrielle.
La deuxième révolution industrielle
La deuxième révolution industrielle, à la fin du 19ème siècle, a amené la production de masse grâce à l’électricité et à l’assemblage à la chaîne. Les capacités de production ont considérablement augmenté et les coûts ont baissé, ce qui a rendu les produits manufacturés accessibles à une plus grande partie de la population.
La troisième révolution industrielle
Il s’agit de la révolution numérique qui a commencé dans les années 1970. L’avènement de l’électronique et des ordinateurs a permis l’automatisation de la production. La robotique et l’apparition de systèmes de gestion de la production assistés par ordinateur ont encore augmenté la production qui devient également plus flexible et plus efficace.
La quatrième révolution industrielle
La quatrième révolution, l’industrie 4.0, représente une évolution encore plus radicale que les trois précédentes. Des technologies de rupture, comme l’Internet des objets (IoT), l’intelligence artificielle (IA), le big data, la réalité augmentée, la réalité virtuelle (VR), la robotique avancée, l’impression 3D et bien sûr la cybersécurité permettent de créer des systèmes de production interconnectés, intelligents et capables de s’optimiser.
Désormais, l’ensemble des systèmes industriels sont intégrés et communiquent en temps réel. Les systèmes de production et de gestion ne font plus qu’un au sein de l’entreprise. La flexibilité et l’agilité qui en découlent permettent une personnalisation poussée de la production, qui est ainsi capable de s’adapter rapidement au marché et à la demande.
La sécurité au travail est également améliorée puisque les dispositifs PTI des travailleurs intègrent des capteurs connectés au réseau global de l’entreprise. Les données de santé et de sécurité des travailleurs sont ainsi analysées en temps réel et recoupées avec celles provenant de la chaîne de production et de l’environnement de travail. Les risques peuvent être anticipés, les travailleurs alertés et les accidents évités.
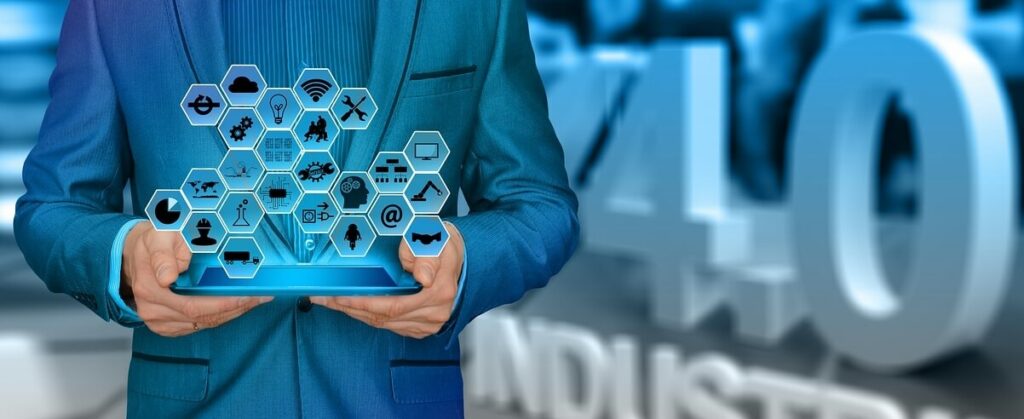
L’IoT au cœur de l’industrie 4.0
L’IoT permet à des composants physiques de production et à des composants numériques de se connecter et d’interagir. Il est ainsi possible de construire un réseau intelligent, de mettre en place un grand nombre d’automatisations et d’améliorer l’efficacité du système de production.
Une usine intelligente
Grâce à l’IoT, une usine traditionnelle peut être transformée en usine intelligente. Chaque capteur, chaque machine, est capable de collecter et analyser des données. Elles peuvent être analysées en temps réel et être utilisées pour optimiser les processus de production.
Des plateformes analysent les données en continu. Elles peuvent concerner le fonctionnement des machines de production, la consommation énergétique ou encore la qualité des produits. Des logiciels spécialisés peuvent ainsi être alimentés et apporter une précieuse aide à la décision. De nombreux paramètres critiques peuvent être pris en compte. La température d’une machine, le niveau d’usure des outils ou des données environnementales peuvent par exemple indiquer que des paramètres peuvent être ajustés automatiquement ou bien qu’une intervention de maintenance doit être programmée. Les temps d’arrêt peuvent ainsi être optimisés et la productivité globale maximisée.
Une application à de nombreux domaines
L’IoT s’applique à l’ensemble des domaines de l’industrie. Grâce à la maintenance prédictive, la production peut être optimisée et la longévité des équipements grandement prolongée. La chaîne logistique peut également être grandement améliorée grâce à des capteurs suivant les matériaux tout au long de la chaîne d’approvisionnement. La gestion des stocks est simplifiée, le suivi de la qualité des produits plus précis. Enfin, la satisfaction client est également améliorée grâce à des délais de fabrication et de livraison plus courts et plus fiables. Les produits peuvent également être davantage personnalisés avec l’ajustement des lignes de production. L’industrie 4.0 est donc capable de produire en masse des produits sur mesure.
Une amélioration de la sécurité des travailleurs
Des capteurs IoT peuvent également être utilisés pour améliorer la sécurité des travailleurs. Les dispositifs PTI connectés apportent une surveillance en temps réel de la santé des travailleurs et de la qualité de l’environnement dans lequel ils évoluent. Surveillance des signes vitaux ou des signes d’incidents, détection de gaz dangereux en temps réel deviennent des applications courantes.
Enfin, l’impact environnemental de l’industrie 4.0 est beaucoup mieux contrôlé. La consommation d’énergie tout comme l’émission de gaz à effet de serre peuvent être réduites, ainsi que la quantité de déchets produits.
Manufacturing 4.0, une production intelligente et agile
Le concept de manufacturing 4.0 révolutionne la production classique. Les principales caractéristiques du système de production deviennent à présent l’agilité et l’intelligence. Grâce à l’intégration au sein même du système de production d’outils comme l’intelligence artificielle, la robotique adaptative ou encore l’impression 3D, le manufacturing 4.0 constitue un environnement capable de s’adapter rapidement et efficacement aux changements des besoins du marché et des clients.
Une plus grande modularité
Le manufacturing 4.0 intègre des systèmes modulaires et robotiques. Ces derniers permettent d’adapter les lignes de production rapidement et facilement. Ces adaptations peuvent être réalisées en quelques heures au lieu de plusieurs jours ou semaines dans une configuration classique. Des produits nouveaux, ou totalement personnalisés, peuvent ainsi être produits en masse en fonction de la demande. Cela apporte une extraordinaire flexibilité aux entreprises.
Une personnalisation de la production
Avec l’impression 3D, il est également possible de réaliser facilement des prototypes ou des petites séries. Réaliser des pièces complexes en petit nombre est impossible en production traditionnelle, à cause des coûts et des délais de fabrication notamment. L’impression 3D permet également aux clients de concevoir directement leurs propres produits. Ils sont ensuite fabriqués à la demande. Cela réduit les coûts, les stocks et les déchets.
La robotique avancée améliore également la sécurité et l’efficacité des travailleurs. Le robot devient collaborateur. Il va prendre en charge les tâches répétitives ou dangereuses et en décharger le travailleur humain. Il va donc également le protéger et étendre ses capacités, afin qu’il puisse se concentrer sur des tâches plus créatives ou stratégiques.
Une connectivité accrue
L’élément essentiel du manufacturing 4.0 est bien entendu la connectivité. Machines, robots, systèmes et produits sont tous connectés les uns aux autres, dans l’usine. Mais la connexion va encore au-delà, intégrant clients et fournisseurs. L’ensemble du système de conception, de production et de vente communique et est coordonné. Tous les acteurs peuvent être informés de façon transparente. La coordination s’en trouve grandement améliorée, tout comme la satisfaction client grâce à la meilleure visibilité sur le système de production.
Avec le manufacturing 4.0, les usines passent d’un lieu de travail et de production à de véritables centres de créativité et d’innovation.
Quelques exemples concrets de l’industrie 4.0
Les avancées technologiques qui ont permis l’essor de l’industrie 4.0 combinent innovation et efficacité opérationnelle. Voici quelques exemples concrets permettant de mieux percevoir les apports de cette nouvelle révolution industrielle.
Une automatisation avancée
Les géants du e-commerce comme Amazon ont très vite intégré des robots pour le tri, l’emballage et l’expédition des produits. Pilotés par une intelligence artificielle, les robots optimisent les itinéraires de collecte des articles dans l’entrepôt, réduisant ainsi les délais d’expédition et de livraison. C’est grâce à cette logistique 4.0 que les clients peuvent recevoir leur commande parfois seulement quelques heures après l’avoir validée.
Du côté des constructeurs automobiles, Tesla a par exemple intégré des robots capables de réaliser des tâches complexes. Ils sont capables par exemple de réaliser des soudures et des assemblages de précision de composants électroniques, tout en s’adaptant aux différents modèles fabriqués.
L’impression 3D appliquée à l’aérospatiale ou à la médecine
L’un des postes de coûts les plus importants pour un avion est sans aucun doute le carburant. Par conséquent, tout ce qui peut alléger l’appareil et faire diminuer sa consommation est un atout. Airbus a mis en place dans ses usines des programmes d’impression 3D afin de produire des pièces sur mesure. C’est un moyen particulièrement efficace de réduire le poids des avions.
L’impression 3D devient également très présente dans le domaine de l’industrie médicale. Des prothèses et des implants sont désormais fabriqués sur mesure en impression 3D. Ils correspondent ainsi exactement aux besoins des patients. Les résultats chirurgicaux ainsi que la récupération des patients s’en trouvent significativement améliorés.
La maintenance prédictive
Siemens a mis en place un processus de maintenance prédictive sur les chaînes de fabrication de turbines à gaz. Des capteurs IoT surveillent en temps réel l’état des machines. Les données recueillies sont analysées afin de prédire les pannes avant qu’elles ne surviennent. Les opérations de maintenance sont programmées à l’avance afin de réduire l’impact sur la production et d’éviter les arrêts imprévus de la production qui sont très coûteux.
La réalité augmentée
La société Bosch a doté ses techniciens de maintenance de lunettes de réalité augmentée. Ils peuvent ainsi bénéficier d’une assistance à distance lors d’opérations délicates. Ils peuvent recevoir des instructions et consulter des documentations et des assistants à tout moment. L’utilisation de ces équipements améliore l’efficacité des interventions et diminue significativement le risque d’erreur.
Pour conclure sur l’industrie 4.0
L’industrie 4.0 est issue de la dernière révolution industrielle, sans aucun doute celle qui aura le plus d’impact sur la société. En intégrant l’intégralité des processus, qu’il s’agisse de la fabrication, de la production, de la logistique ou encore des autres services de l’entreprise, on dispose d’une vision globale. Il est alors plus facile de maîtriser l’ensemble des éléments pouvant interagir entre eux et d’optimiser le fonctionnement et la productivité de l’entreprise. Il s’ensuit une diminution des coûts, une amélioration de la qualité, une personnalisation de la production et une hausse de la satisfaction client.
Outre la productivité, les technologies liées à l’industrie 4.0 permettent également une amélioration de la sécurité des travailleurs. En intégrant des capteurs IoT dans les dispositifs PTI des travailleurs, il est possible de les situer en permanence dans l’écosystème de l’entreprise et de s’assurer de leur santé ainsi que de la qualité de leur environnement.
N’hésitez pas à nous contacter et venez découvrir la dernière innovation DatiPlus 4X. Ce dispositif PTI s’intègre parfaitement à la tenue de vos travailleurs. Il permet de détecter toute situation anormale comme une chute ou une perte de connaissance. Mieux encore, il permet de déclencher automatiquement ou manuellement une alerte en cas de danger, alerte qui peut être transmise quelles que soient les conditions. Ainsi, que vos travailleurs soient dans une zone couverte par un réseau GSM ou non, ils continueront à bénéficier de la meilleure protection possible.
Nos autres Guides
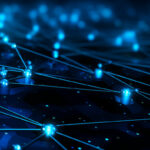
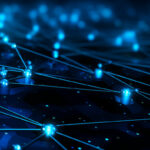
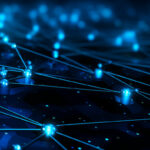
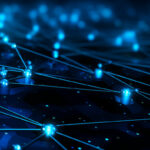
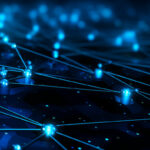